Maintaining the integrity of the rails on which a rail-mounted gantry crane operates is critical for the crane’s performance, safety, and longevity. Over time, these rails can suffer from wear and tear, misalignment, and structural damage, necessitating timely and precise repairs to ensure optimal crane operation. This passage will explore the step-by-step process for diagnosing and fixing issues with the rails of a rail-mounted gantry crane, ensuring that the system remains efficient and safe.
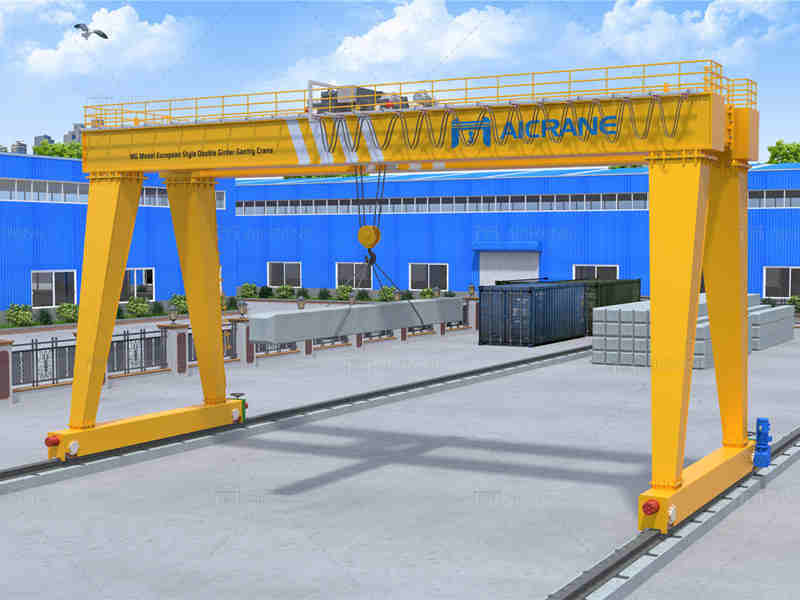
Conducting a Thorough Inspection
The first step in fixing the rails of a rail-mounted gantry crane is to conduct a thorough inspection. Some gantry crane manufacturers will provide tips for inspection. This involves:
Visual Inspection: Look for obvious signs of wear and tear, such as cracks, corrosion, and physical deformation. Check for misalignment and gaps between rail segments.
Measurement: Use measuring tools to check the rail gauge (distance between rails), rail straightness, and levelness. Misalignment or uneven wear can be detected through precise measurements.
Non-destructive Testing (NDT): Methods such as ultrasonic testing or magnetic particle testing can help identify internal flaws or cracks that are not visible to the naked eye.
By identifying the exact nature and location of the problems, you can plan the necessary repairs more effectively.
Planning the Repair Work
Once the inspection is complete, the next step is to plan the repair work. This includes:
Determining the Scope of Work: Based on the inspection results, determine whether the repairs involve minor adjustments, rail replacement, or major structural work.
Gathering Materials and Tools: Ensure you have the necessary materials, such as replacement rail segments, welding equipment, alignment tools, and safety gear.
Scheduling: Plan the repair work during a period of low rail-mounted gantry crane activity to minimize disruptions. Coordinate with other departments if the crane is part of a larger operational system.
Preparing the Work Area
Safety is paramount when repairing rail-mounted gantry crane rails. Proper preparation of the work area involves:
Securing the Crane: Ensure the rail-mounted gantry crane is locked out and tagged out to prevent any accidental movement. Use wheel chocks or other restraints as necessary.
Clearing the Area: Remove any obstructions and ensure the area around the rails is clean and free from debris.
Setting Up Safety Barriers: Erect safety barriers and warning signs to protect workers and prevent unauthorized access to the repair site.
Rail Alignment and Adjustment
Minor misalignments and uneven wear can often be corrected through adjustment:
Realignment: Use hydraulic jacks or alignment tools to shift the rails back into the correct position. Precision is crucial, so use laser alignment systems or other precise measurement tools.
Shimming: If the rail height is uneven, use shims to level the rails. Place the shims under the rail and secure them properly to ensure they do not shift during operation.
Grinding: Smooth out any irregularities or uneven surfaces on the rail using a rail grinder. This helps to ensure a smooth running surface for the rail-mounted gantry crane wheels.
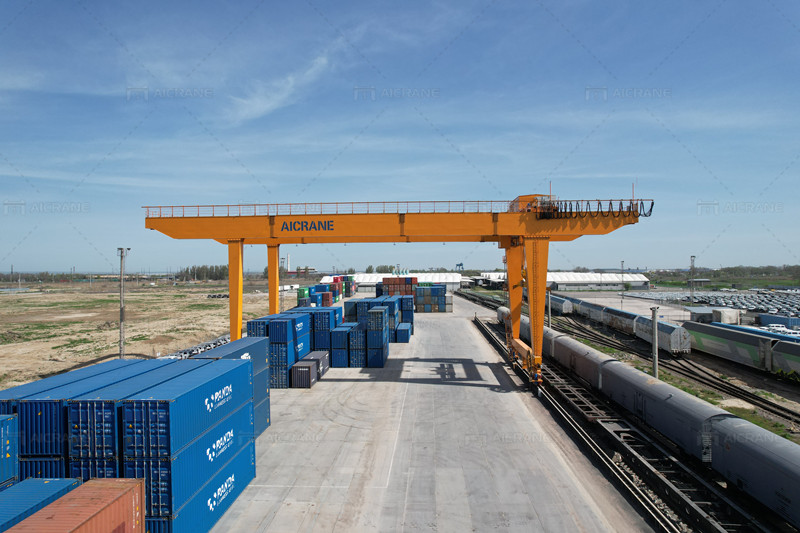
Rail Replacement
In cases where the rails are severely damaged or worn, replacement may be necessary:
Removing the Damaged Rail: Cut and remove the damaged rail sections using cutting torches or rail saws. Be cautious to prevent damage to the surrounding infrastructure.
Installing New Rails: Position the new rail segments in place, ensuring they are properly aligned with the existing rails. Use rail joiners and welding to secure the segments together.
Securing the Rails: Fasten the new rail sections to the sleepers or ties using appropriate fasteners. Ensure that the rail is firmly secured and does not have any play or movement.
Welding and Joint Repair
Rail joints are critical points that often require attention:
Welding: Use proper welding techniques to join rail segments. Ensure the welds are strong and smooth to avoid creating weak points or bumps.
Grinding Welds: After welding, grind the welds to ensure they are flush with the rail surface. This prevents bumps that can cause uneven rail-mounted gantry crane movement.
Testing and Calibration
After completing the repairs, thorough testing and calibration are necessary:
Load Testing: Perform load tests to ensure the repaired rails can handle the weight and stress of the rail-mounted gantry crane operation. This helps to identify any weaknesses or potential failures.
Operational Testing: Run the rail-mounted gantry crane along the repaired rails to check for smooth operation. Look for any signs of misalignment, vibration, or unusual noise.
Calibration: Fine-tune the alignment and ensure that the rail gauge, levelness, and straightness meet the required specifications.
Regular Maintenance and Monitoring
Preventive maintenance is key to avoiding future rail issues:
Routine Inspections: Schedule regular inspections to catch early signs of wear and tear. This allows for timely maintenance before problems escalate.
Lubrication: Keep the rail surfaces and rail-mounted gantry crane wheels properly lubricated to reduce friction and wear.
Cleaning: Regularly clean the rail surfaces to prevent debris buildup, which can cause uneven wear and damage.
Documentation and Reporting
Maintain detailed records of all inspections, repairs, and maintenance activities:
Inspection Reports: Document the findings of each inspection, noting any issues identified and their severity.
Repair Logs: Keep detailed logs of all repair work performed, including materials used, methods employed, and personnel involved.
Maintenance Records: Track all routine maintenance activities, including lubrication schedules, cleaning, and adjustments.
Proper documentation helps in tracking the condition of the rails over time and provides valuable information for future maintenance planning.
Training and Safety Compliance
Ensure that all personnel involved in rail maintenance are properly trained:
Training Programs: Provide training on rail inspection, repair techniques, safety protocols, and the use of specialized tools and equipment.
Safety Compliance: Adhere to all relevant safety standards and regulations to protect workers and ensure a safe working environment.
Maintaining and fixing the rails of a rail-mounted gantry crane is a comprehensive process that involves careful inspection, precise planning, and diligent execution. By following these steps, operators can ensure the continued efficiency and safety of their crane operations. Regular maintenance and proactive monitoring are essential to prevent costly downtime and extend the lifespan of both the crane and its rail infrastructure. Proper training and adherence to safety standards are crucial to safeguarding the well-being of maintenance personnel and ensuring the smooth operation of rail-mounted gantry cranes.